DOYLE DESIGN
The innovators behind the leading Cableless Technology and where sailmaking boundaries are redefined.
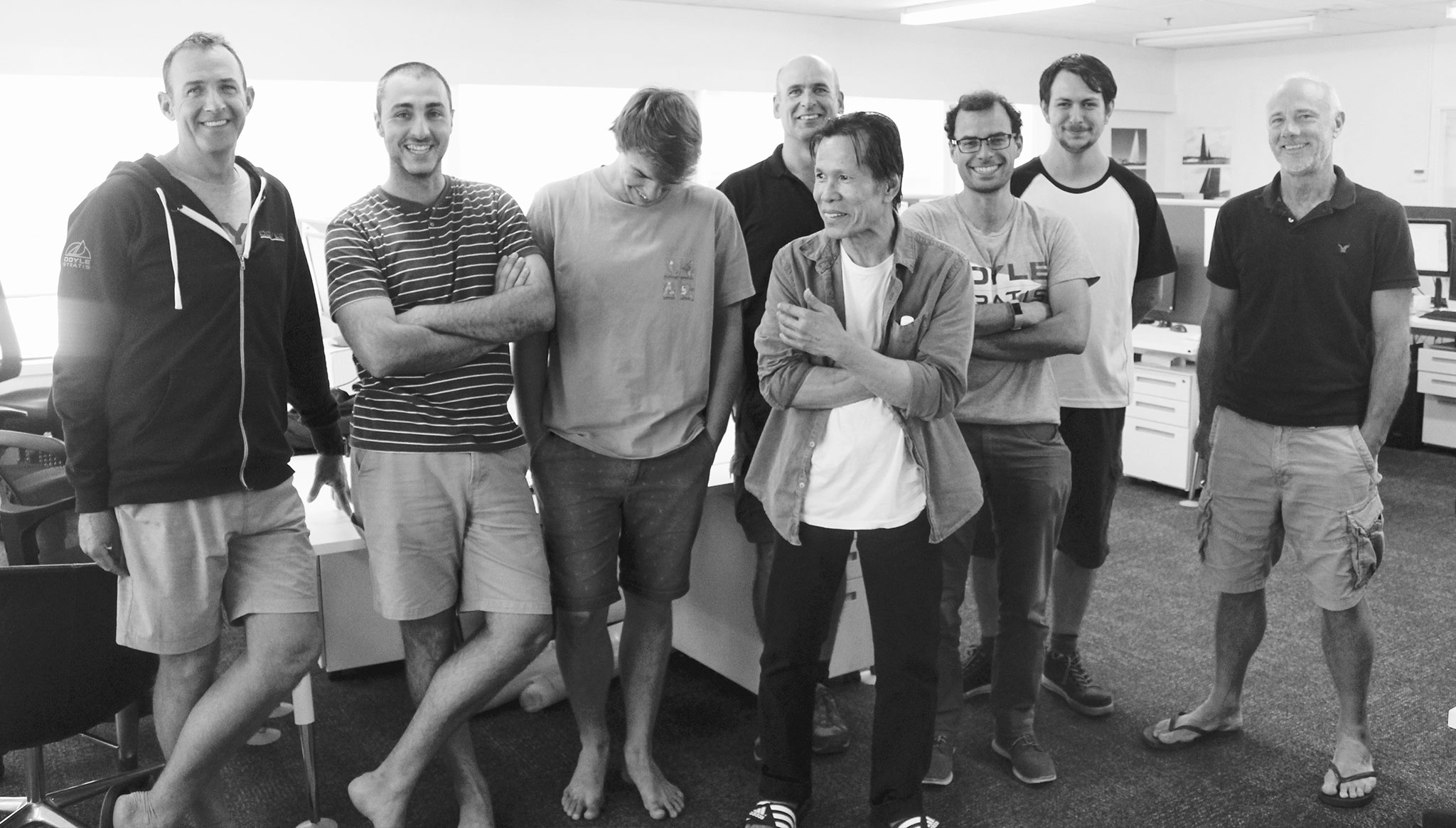
Doyle Sails' central design team consists of highly qualified sailors who each bring different strengths. Our unique design software and tools are amongst the most advanced 3D modelling and air flow technology available worldwide.
One of the cornerstones of our sailmaking process is a sophisticated and thorough approach to design and engineering. Before any fibre gets laid or cloth is cut, we complete a detailed analysis of the boat, the rig and hardware to fully understand what will be required to make sails that will fulfill the customer's requirements. This approach, in combination with design expertise, has given us the confidence and experience to take on some of the biggest and most complex yacht projects.
“The design team led by Richard Bouzaid, put in a huge effort. If you want something different, something fast or an edge - it is best not to follow the crowd”.
- Alex Thomson, Hugo Boss Vendee Globe 2016/17
One of the cornerstones of our sailmaking process is a sophisticated and thorough approach to design and engineering. Before any fibre gets laid or cloth is cut, we complete a detailed analysis of the boat, the rig and hardware to fully understand what will be required to make sails that will fulfill the customer's requirements. This approach, in combination with design expertise, has given us the confidence and experience to take on some of the biggest and most complex yacht projects.
“The design team led by Richard Bouzaid, put in a huge effort. If you want something different, something fast or an edge - it is best not to follow the crowd”.
- Alex Thomson, Hugo Boss Vendee Globe 2016/17
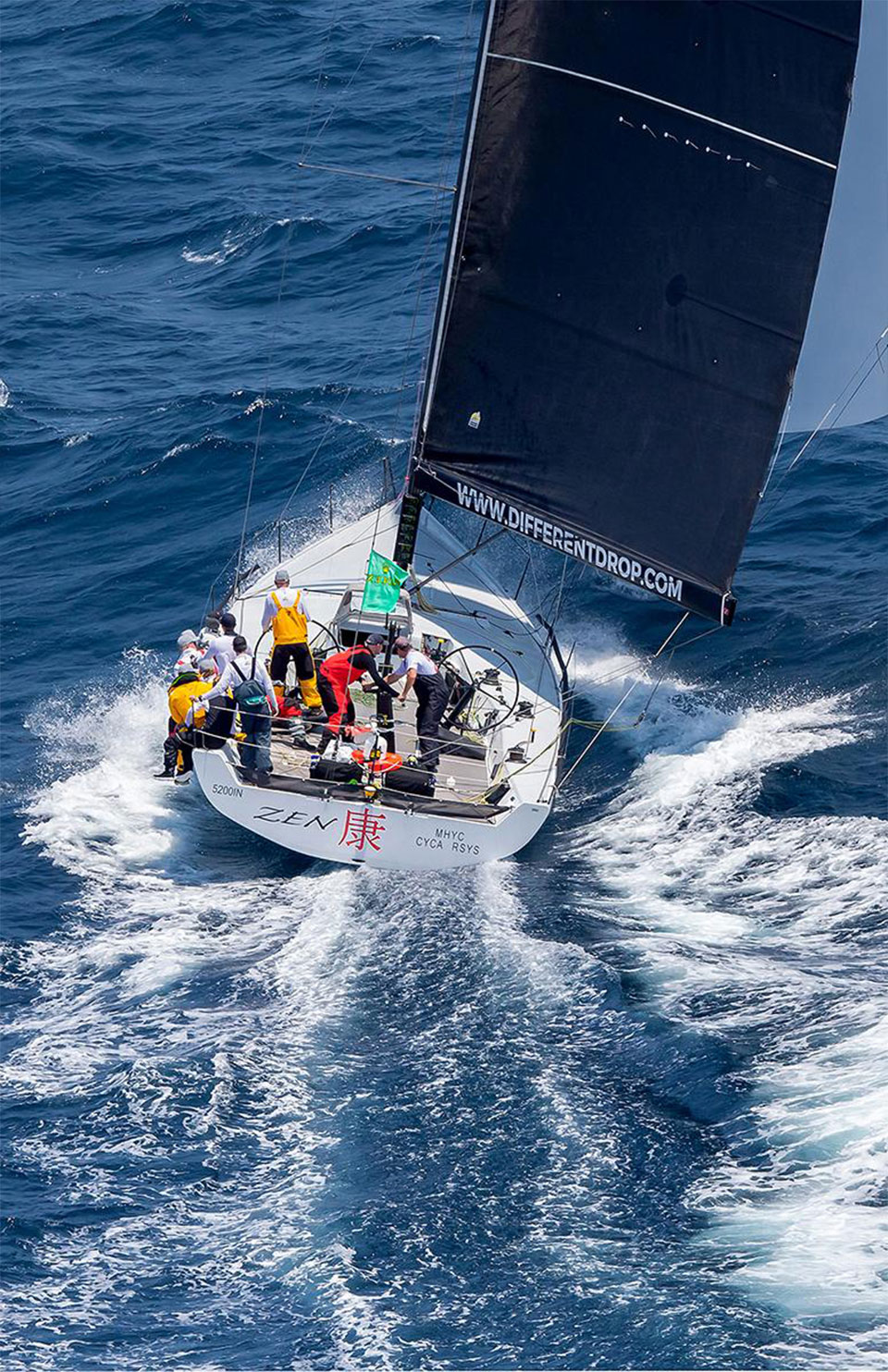
GLOBAL DESIGN NETWORK
Doyle's Head of Design Richard Bouzaid leads the innovation and research for Doyle’s Design Department. With over 20 years of sailing experience, Bouzaid has been involved in winning campaigns for the America’s Cup, Volvo Ocean Race, Vendee Globe and several Grand Prix projects.
Recognising each sail yacht has its particular set of unique characteristics, the designers at Doyle draws on a worldwide pool of veteran sailors and design technology, as well as exclusive Doyle fabrics, proprietary sail design software and wind tunnel testing. This technology is why Doyle’s sails are known to be strong, durable and hold their shape across the wind range.
Doyle's Design team utilize the world-leading sail design software called SailPak. This sophisticated sailmaking package includes everything from the early design stages, full structural engineering and aerodynamic characteristics to creating a file that will instruct the machines exactly how to construct the material. Taking the 3-dimensional output from SailPak, Doyle’s engineers and CFD analysts can trim the sails for the design team. Coupled with FEA (Finite Element Analysis), this process determines optimal cloth characteristics or fibre layouts for laminate sails.
Having solved some of the most challenging superyacht projects and high-performance grand-prix sails, our innovative engineers are accustomed to creating uniquely effective construction methods, sail handling systems, battens, batten systems, head, tack and clew attachments. Doyle solutions are highly engineered and elegant.
Doyle Sails proudly boasts a team of 15 designers based out of New Zealand, Australia, United States of America, Italy and others. Co-ordinated by Paul Stubbs, this team works closely together to design, develop and remain consistent in the Doyle Sails approach globally.
New Zealand caters to all requirements from Optimist to Superyacht and is project lead on most of the Grand Prix and Superyacht projects that Doyle Sails is proudly associated with. The team consists of Richard Bouzaid (Design Director), Paul Stubbs (Design Co-ordinator), Justin Ferris, Daniel Fong, Stefano Nava.
Australia: Andrew Lechte (One Design Specialist)
United States of America is home to the CFD specialists with Tyler Doyle, Duncan Swain, Travis Meindl and Dave Armitage all experts in Coastal, Race and Grand Prix designs.
Italy is home to three sail designers who work cohesively with the team in New Zealand to deliver high quality and performance sails for the Grand Prix and Superyacht yachts. The Italian based team consists of Dario Motta, Alessandro Castelli and Nino Cirello.
New Zealand caters to all requirements from Optimist to Superyacht and is project lead on most of the Grand Prix and Superyacht projects that Doyle Sails is proudly associated with. The team consists of Richard Bouzaid (Design Director), Paul Stubbs (Design Co-ordinator), Justin Ferris, Daniel Fong, Stefano Nava.
Australia: Andrew Lechte (One Design Specialist)
United States of America is home to the CFD specialists with Tyler Doyle, Duncan Swain, Travis Meindl and Dave Armitage all experts in Coastal, Race and Grand Prix designs.
Italy is home to three sail designers who work cohesively with the team in New Zealand to deliver high quality and performance sails for the Grand Prix and Superyacht yachts. The Italian based team consists of Dario Motta, Alessandro Castelli and Nino Cirello.
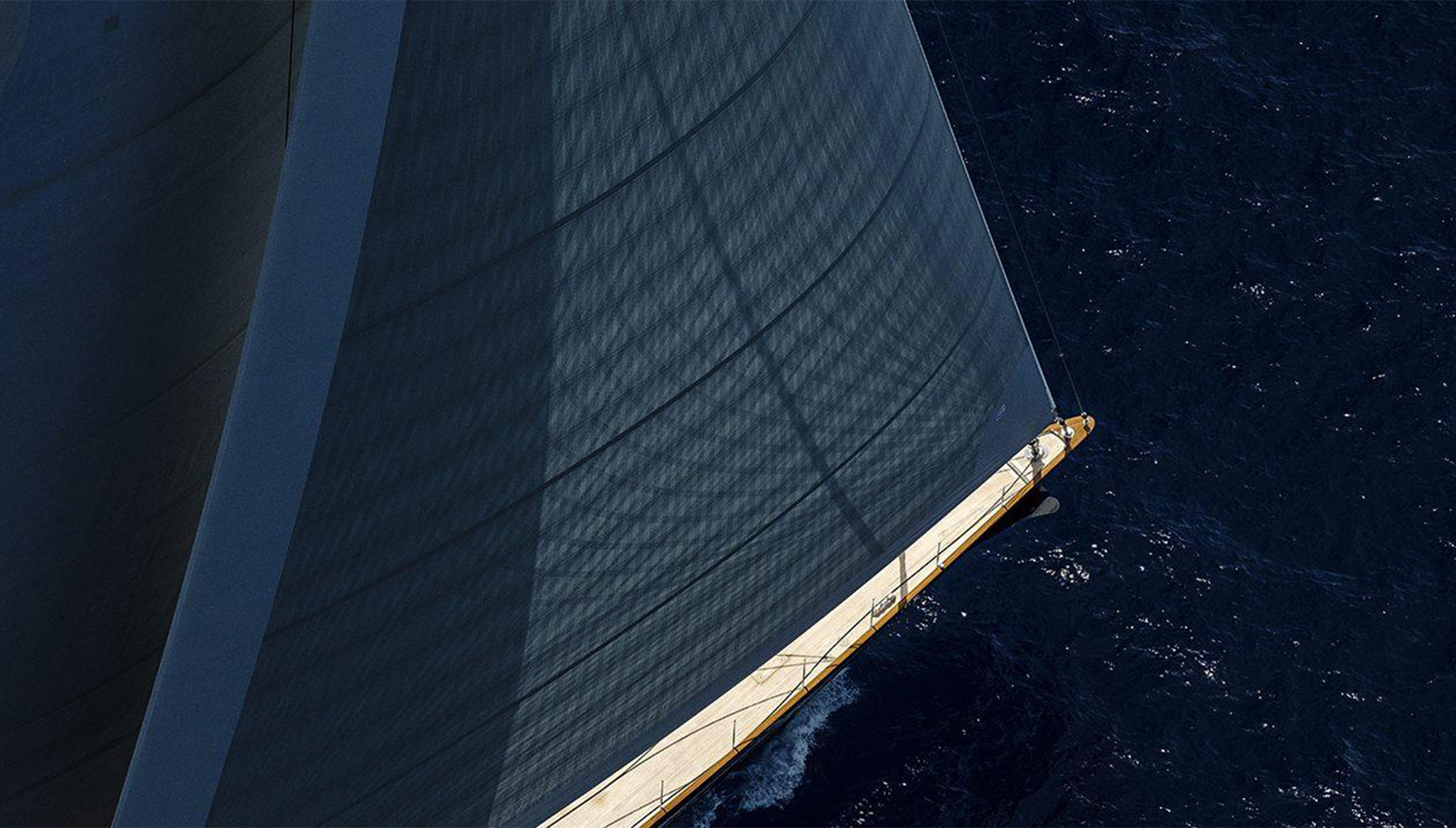
WHAT IS CFD?
Doyle CFD uses high resolution simulations to optimize sailing yacht aerodynamics, hydrodynamics and structures. Our analysis and designs are driven by data from state-of-the-art Computational Fluid Dynamic (CFD) and Finite Element Analysis (FEA) simulations. Our simulations provide designers with much of the same data supplied by wind tunnels and tow tanks and a lot more. We have experience analyzing and designing most major sailing yacht components from sails to foils. Doyle CFD was founded in 2011 to further develop computational tools and analysis techniques developed at Stanford University, NASA and Doyle Sails. Doyle Sails was one of the early adopters of this type of in depth sail study and this technology plays a major role in the design of all Doyle super yacht sails.
Images shown below display CFD and FEA studies on two of the world’s largest sailing yachts; M5 and Sailing Yacht A. On top is shown aerodynamic and hydrodynamic post processing from a CFD based VPP study of M5 sail options. In the middle are fiber layouts from Sailing Yacht A’s mainsail and below that stress plots from analyzing the sail and rig. On the bottom is shown a typical super yacht sail plan and to the right of that M5 sailing.
HOW IT WORKS...
A CFD analysis begins by creating a geometric model of the mast, boom, hull, deck, sails and other features that are important to the flow around the boat. What geometry is included depends on the required level of resolution of the study. A structural FEA model begins by defining the geometry and structural properties of the mast, sails, boom, running rigging and their connections. Once the geometry and structural properties are defined fluid flow and structural loads are applied to the models. CFD simulations provide detailed information about the air and water flow around the boat as well as the pressure and skin friction on the sails, hull and foils. CFD simulations are used to optimize shapes. FEA simulations predict the state of stress and deformation in the sails, battens, mast and rigging and are used by designers to determine how strong structures need to be.
CFD and FEA simulations can be combined in a Fluid Structure Interaction (FSI) model, which combines a fluid flow solver and a finite element solver. FSI models are used to predict the flying shape of sails. The FSI solver performs the calculation using iterative steps in a loop process; for each loop the aerodynamic forces are calculated and then applied to the sail which deforms into a new shape. The new shape is then used in the next loop to recalculate the aerodynamic forces and then recalculate the deformed shape. The computation is done in this iterative form until the discrepancy between the deformed shape of the current step and the one of the previous step is reduced below a threshold.
Sail designers use sail strain maps that are produced in FSI or FEA models to analyze and to verify the structural behavior of the fiber layout. Highly loaded regions characterized by excessive strain are reinforced with additional fiber to better support these regions. Individual yarn strains are analyzed to determine where and how the loads are transmitted, so that the fiber layouts can be developed to control and optimize the shape of the sail. The sail design is tested through its range of use to confirm that no excessive strain is generated and the flying shape is optimized to suit each condition.
CFD and FEA simulations can be combined in a Fluid Structure Interaction (FSI) model, which combines a fluid flow solver and a finite element solver. FSI models are used to predict the flying shape of sails. The FSI solver performs the calculation using iterative steps in a loop process; for each loop the aerodynamic forces are calculated and then applied to the sail which deforms into a new shape. The new shape is then used in the next loop to recalculate the aerodynamic forces and then recalculate the deformed shape. The computation is done in this iterative form until the discrepancy between the deformed shape of the current step and the one of the previous step is reduced below a threshold.
Sail designers use sail strain maps that are produced in FSI or FEA models to analyze and to verify the structural behavior of the fiber layout. Highly loaded regions characterized by excessive strain are reinforced with additional fiber to better support these regions. Individual yarn strains are analyzed to determine where and how the loads are transmitted, so that the fiber layouts can be developed to control and optimize the shape of the sail. The sail design is tested through its range of use to confirm that no excessive strain is generated and the flying shape is optimized to suit each condition.